Holton 345 Redux
- the elephant
- Posts: 3378
- Joined: Thu Aug 13, 2020 8:39 am
- Location: 404 - Not Found
- Has thanked: 1896 times
- Been thanked: 1335 times
Re: Holton 345 Redux
MTS EXTENDED! It plays GREAT for me now. It was always a good tuba — in ways — but it came saddled with a lot of problems that I thought I could fix myself. (I had no idea about the horrors hidden within the joints of that bugle at that time, though. No one but the builder did.)
With all the acoustic alterations I have made (with the assistance of Rob Carpenter and Tom Treece) I started to worry that I had maybe overdone it and messed up the horn.
Nope. It's fine, and almost every issue it had when I traded my Alex for it is now eliminated or greatly improved. It isn't perfect but (for me) is now a lot of fun to play at work.
With all the acoustic alterations I have made (with the assistance of Rob Carpenter and Tom Treece) I started to worry that I had maybe overdone it and messed up the horn.
Nope. It's fine, and almost every issue it had when I traded my Alex for it is now eliminated or greatly improved. It isn't perfect but (for me) is now a lot of fun to play at work.
- These users thanked the author the elephant for the post:
- TheBerlinerTuba (Tue Oct 11, 2022 5:02 am)

- LargeTuba
- Posts: 777
- Joined: Thu Aug 13, 2020 11:08 am
- Has thanked: 97 times
- Been thanked: 136 times
Re: Holton 345 Redux
Would you do the plating prep yourself?
I’ve inquired with a couple people about the cost of plating. Estimates have widely ranged, but all in the 4k+ range.
I’ve inquired with a couple people about the cost of plating. Estimates have widely ranged, but all in the 4k+ range.
- These users thanked the author LargeTuba for the post:
- the elephant (Mon Oct 10, 2022 8:36 pm)
Pt-6P, Holton 345 CC, 45slp
- the elephant
- Posts: 3378
- Joined: Thu Aug 13, 2020 8:39 am
- Location: 404 - Not Found
- Has thanked: 1896 times
- Been thanked: 1335 times
Re: Holton 345 Redux
I would do the prep, yes. (I've done it a lot in the past, and the valve section will not be on the horn, so it will be relatively easy. I plan on having Anderson's do the work — IF — I go that route. It is still a big "if", too. But I *am* considering it. (In the past I was very much against it.)

-
- Posts: 1432
- Joined: Thu Aug 13, 2020 10:39 pm
- Location: SoCal
- Has thanked: 1553 times
- Been thanked: 467 times
Re: Holton 345 Redux
Excellent work and I like the special guest in the video.
Isn't that a bit like @bort2.0 saying he's found his forever tuba?
A bit of good natured ribbing of two good natured people.
Elephant said "I do not see myself wanting to change anything else, ever."


- These users thanked the author York-aholic for the post:
- the elephant (Mon Oct 10, 2022 10:27 pm)
Some old Yorks, Martins, and perhaps a King rotary valved CC
- the elephant
- Posts: 3378
- Joined: Thu Aug 13, 2020 8:39 am
- Location: 404 - Not Found
- Has thanked: 1896 times
- Been thanked: 1335 times
- arpthark
- Posts: 3899
- Joined: Mon Aug 24, 2020 4:25 pm
- Location: Southeastern Connecticut
- Has thanked: 951 times
- Been thanked: 1067 times
- Contact:
Re: Holton 345 Redux
@the elephant, wasn't this tuba formerly silver? If so, when/why did you strip it?
- These users thanked the author arpthark for the post:
- the elephant (Tue Oct 11, 2022 8:48 am)
Blake
Bean Hill Brass
Bean Hill Brass
- cjk
- Posts: 695
- Joined: Thu Aug 13, 2020 11:46 am
- Location: Atlanta, GA
- Has thanked: 264 times
- Been thanked: 147 times
Re: Holton 345 Redux
If that were my tuba, I think I'd keep it raw brass. I'd just skip that labor and expense. To my eyes, it wouldn't be prettier than it is now.the elephant wrote: ↑Mon Oct 10, 2022 8:36 pm I would do the prep, yes. (I've done it a lot in the past, and the valve section will not be on the horn, so it will be relatively easy. I plan on having Anderson's do the work — IF — I go that route. It is still a big "if", too. But I *am* considering it. (In the past I was very much against it.)
I'm very happy for you that you've remade that tuba into what you've wanted it to be. That's very exciting.
- These users thanked the author cjk for the post:
- the elephant (Tue Oct 11, 2022 8:47 am)
- the elephant
- Posts: 3378
- Joined: Thu Aug 13, 2020 8:39 am
- Location: 404 - Not Found
- Has thanked: 1896 times
- Been thanked: 1335 times
Re: Holton 345 Redux
It was a factory BBb 340 in silver, and most of the remaining factory plating had worn off. Bob Rusk had it replated after he cut and rebuilt it.
So far as the various witness marks tell me, the bell and bottom bow were plated off the horn. The existing plating was not removed first so that a fresh strike coat of copper could be plated to the brass; the new silver did not fully adhere to the old silver and was peeling off badly in spots.
I do not see evidence of the top bow or inner branches having been replated. And about 45% of the factory silver was worn off. Even the copper strike coating was mostly gone, so there was just a lot of bare brass with a few pink copper patches peeking through.
Most of the work I did to the horn at first was to take the incorrectly-sized rotor out of the leadpipe and replace the leadpipe with something that was far less "++ungood". (The leadpipe was laughably bad.) The old 5th slide was soldered to the bell, so removing it left solder pads. The new one had to be routed from the MTS over to the same place on the bell but pointed upwards, and I used three small braces to secure it. The old leadpipe left marks, too, as I had to adjust where it sat on the bell.
Later, all this was removed and I had to take apart the bugle to fix all the wretched joint work and re-taper all the ends of the six branches. Stretching the ends of the cut branches to make them fit into the ferrules required a lot of annealing.
So, with all the solder pads on the bell and bottom bow, all the burned-off silver from the annealing, and the factory silver on the top bow and inner branches being about 50% gone… well… the tuba looked like garbage.
I sanded it all off, painstakingly, and slowly, using finger pressure only, and wet 400 to 1000 grit sandpaper used for automotive painting. As soon as I saw yellow in the gray slush on the paper I moved on. I think by doing it this way I removed very little brass, but it is something I will *never* do again. It took me the better part of two weeks to do everything this carefully. And even then I did not do the inside of the bell because of how thin it might end up being at the engraved section just below the flare. It was crushed there at some point in the past, and there is some metal memory at play, and it is thin there, so I do not want to make that section any thinner at all for any reason. When I had to sand down the silver inside the bell I thought of this and decided to just leave it be. (If I have it plated I will take it to Anderson's in person and stay in a hotel while it is being done. That way I can talk to the person who will do the work and discuss options for that section of the bell.)
tl;dr version — The silver was worn off in large patches when I got the tuba. The replating was done poorly, so it was peeling off, and it was pretty much impossible to not ruin it with the torch. After all the work I had done, when I had it completely taken apart I decided to remove what was left, as the tuba would probably look much better like that when it was finished.
Here is an album of annotated photos of that process. Take a look at page 2 — omg…!
https://elephant.smugmug.com/RuskRemover/n-XwCrHd/
This photo is from that album…

- These users thanked the author the elephant for the post (total 2):
- arpthark (Tue Oct 11, 2022 9:45 am) • York-aholic (Tue Oct 11, 2022 7:29 pm)

- bort2.0
- Posts: 5253
- Joined: Thu Aug 13, 2020 9:13 am
- Location: Minneapolis
- Has thanked: 336 times
- Been thanked: 999 times
Re: Holton 345 Redux
Zing!York-aholic wrote: ↑Mon Oct 10, 2022 10:06 pm Excellent work and I like the special guest in the video.
Elephant said "I do not see myself wanting to change anything else, ever."Isn't that a bit like @bort2.0 saying he's found his forever tuba?
A bit of good natured ribbing of two good natured people.
I was really excited to read that from Wade as well. Definitely thought he was kind of crazy for doing all this, taking it apart and reassembling so many times, and wondering when or if it would actually ever be finished. Apparently it's not actually finished, in terms of the finish itself has not been applied, but a spectacular result for this tuba.
One of the most interesting things to me, is that so many people probably would have just used this to but exactly as it was, and just dealt with it. And it probably would have been fine, but it's just so much more to have it done the right way all around. Kind of like a minor renovation to a bathroom versus ripping everything down to the studs and starting over.
Wade, congratulations! Now for God's sake don't start another one of these. :-)
- These users thanked the author bort2.0 for the post:
- the elephant (Tue Oct 11, 2022 9:38 am)
- the elephant
- Posts: 3378
- Joined: Thu Aug 13, 2020 8:39 am
- Location: 404 - Not Found
- Has thanked: 1896 times
- Been thanked: 1335 times
Re: Holton 345 Redux
I have essentially "blueprinted" all three of my horns (as much as possible) and then heavily modified or completely scratch-built large sections of them.
I have several other projects in the wings but cannot afford to start them until my wife gets a new job. (It has been since August of 2020, so things are tight AF for us right now.) All of these project horns need a lot of parts. Some will be already-known winners, and some will be completely experimental. This is my hobby and avocation so I put a lot into this stuff. I am as interested in the process as I am in the results.
Here are some of the things I have on the catapult at "Ready 5"…
King K-90 GG Contrabass Bugle — 5-rotor CC tuba, for me
King K-90 GG Contrabass Bugle — 4-piston GG tuba, for me
Meinl-Weston 182 F tuba — hoping for a small, 621-like F with a nicer sound, for me
Conn 24J — raw brass restoration, to sell
Conn 24J — 5 rotor BBb with Siegfried bell, to sell
Getzen GG "Baby" Contrabass Bugle — something very small in F, to sell
Olds Ultratone GG Contrabass Bugle — Something fun to play that is the same size as the Olds O-99, to sell
Couesnon Eb — 5 valved Eb or F, not sure, maybe to sell
King K-80 G Euphonium Bugle — I have five; two will be a tenor tubas. (I owe Cam Brook one and keep forgetting!)
J.W. Pepper euphonium bell (19th century) — Cimbasso in CC, for me (just farting around)
I have lots more, too. However, I do not think I will be all that worried about being this meticulous with any of these, as I will never have to appear onstage with any of them. (We place questionnaires in our programs to poll audiences on various things. This has been a really great and productive practice since we started it in 1996. Unfortunately, our older patrons like to carp about violinists' shoes not being properly polished, poor musicians who happen to have bad haircuts, or the tuba player not polishing his horns. We had someone criticize the tuxedo worn by our assistant concertmaster as being poorly fitted and "tatty". Yes, I am serious about that. Behold, the modern patron of classical music…)
I also have four molded plastic hard cases to tear down and rebuild to fit my horns, with far better protection than what these el cheapo plastic cases normally offer. I also have one vintage wood-shell Mirafone case that is just the two wooden halves. I intend to make a fiberglass-shelled case for my 1971 186 with ATA hardware and padding purchased from Anvil so that I can ride the bus to runouts rather than drive as I have to do today. (I have to drive my Jeep Wrangler for six hours today because I do not have a hard case set up for the Holton 345. I have it stripped clean and ready to rebuild but am currently "cash-poor" so I could not purchase the padding and liner material. I will get this built over the winter in time for our Spring runouts, though. With only one working vehicle, my wife will be trapped at home for twelve hours today without any working vehicle. Now that I mention it, I have to do some major work on two cars, as well. This crap never seems to end, heh, heh…)
I have several other projects in the wings but cannot afford to start them until my wife gets a new job. (It has been since August of 2020, so things are tight AF for us right now.) All of these project horns need a lot of parts. Some will be already-known winners, and some will be completely experimental. This is my hobby and avocation so I put a lot into this stuff. I am as interested in the process as I am in the results.
Here are some of the things I have on the catapult at "Ready 5"…
King K-90 GG Contrabass Bugle — 5-rotor CC tuba, for me
King K-90 GG Contrabass Bugle — 4-piston GG tuba, for me
Meinl-Weston 182 F tuba — hoping for a small, 621-like F with a nicer sound, for me
Conn 24J — raw brass restoration, to sell
Conn 24J — 5 rotor BBb with Siegfried bell, to sell
Getzen GG "Baby" Contrabass Bugle — something very small in F, to sell
Olds Ultratone GG Contrabass Bugle — Something fun to play that is the same size as the Olds O-99, to sell
Couesnon Eb — 5 valved Eb or F, not sure, maybe to sell
King K-80 G Euphonium Bugle — I have five; two will be a tenor tubas. (I owe Cam Brook one and keep forgetting!)
J.W. Pepper euphonium bell (19th century) — Cimbasso in CC, for me (just farting around)
I have lots more, too. However, I do not think I will be all that worried about being this meticulous with any of these, as I will never have to appear onstage with any of them. (We place questionnaires in our programs to poll audiences on various things. This has been a really great and productive practice since we started it in 1996. Unfortunately, our older patrons like to carp about violinists' shoes not being properly polished, poor musicians who happen to have bad haircuts, or the tuba player not polishing his horns. We had someone criticize the tuxedo worn by our assistant concertmaster as being poorly fitted and "tatty". Yes, I am serious about that. Behold, the modern patron of classical music…)
I also have four molded plastic hard cases to tear down and rebuild to fit my horns, with far better protection than what these el cheapo plastic cases normally offer. I also have one vintage wood-shell Mirafone case that is just the two wooden halves. I intend to make a fiberglass-shelled case for my 1971 186 with ATA hardware and padding purchased from Anvil so that I can ride the bus to runouts rather than drive as I have to do today. (I have to drive my Jeep Wrangler for six hours today because I do not have a hard case set up for the Holton 345. I have it stripped clean and ready to rebuild but am currently "cash-poor" so I could not purchase the padding and liner material. I will get this built over the winter in time for our Spring runouts, though. With only one working vehicle, my wife will be trapped at home for twelve hours today without any working vehicle. Now that I mention it, I have to do some major work on two cars, as well. This crap never seems to end, heh, heh…)

- arpthark
- Posts: 3899
- Joined: Mon Aug 24, 2020 4:25 pm
- Location: Southeastern Connecticut
- Has thanked: 951 times
- Been thanked: 1067 times
- Contact:
Re: Holton 345 Redux
What happened to the Ab tenor tuba from a few years ago? https://yorkmaster.org/yorkmaster/photo ... index.htmlthe elephant wrote: ↑Tue Oct 11, 2022 10:28 am Here are some of the things I have on the catapult at "Ready 5"…
King K-90 GG Contrabass Bugle — 5-rotor CC tuba, for me
King K-90 GG Contrabass Bugle — 4-piston GG tuba, for me
Meinl-Weston 182 F tuba — hoping for a small, 621-like F with a nicer sound, for me
Conn 24J — raw brass restoration, to sell
Conn 24J — 5 rotor BBb with Siegfried bell, to sell
Getzen GG "Baby" Contrabass Bugle — something very small in F, to sell
Olds Ultratone GG Contrabass Bugle — Something fun to play that is the same size as the Olds O-99, to sell
Couesnon Eb — 5 valved Eb or F, not sure, maybe to sell
King K-80 G Euphonium Bugle — I have five; two will be a tenor tubas. (I owe Cam Brook one and keep forgetting!)
J.W. Pepper euphonium bell (19th century) — Cimbasso in CC, for me (just farting around)
I say "a few years ago" but 2011 was 11 years ago. Yikes!
edit: nevermind, I see that you mentioned the King K-80 in your post. I assume that is what you cut to Ab?
Blake
Bean Hill Brass
Bean Hill Brass
- the elephant
- Posts: 3378
- Joined: Thu Aug 13, 2020 8:39 am
- Location: 404 - Not Found
- Has thanked: 1896 times
- Been thanked: 1335 times
Re: Holton 345 Redux
The K-80 will stay in G. It was well-designed and plays well at that length.
The Getzen could not be cut short enough to put it into Ab without using an overly-large-bore valve section. It will stay in G so I can use valves that will make sense. I have thought to lower it to F and use .689" King pistons, which might work well. In Ab that would end up having valves that are larger than .750" — I'm too stupid to work that out into a working horn, heh, heh…
My desire to do this is to put an instrument in the tenor or bass tuba range that is as close as possible to G#/Ab minor. A CC tuba plays well in A, D, G, and C minor, so those fingering patterns in relation to the "home key" of the horn would make the chances of a homemade instrument being reasonably in tune and easily correctable if it is not. Building a Bb euphonium from scratch using and bell and tubing intended for something else would likely net a horn that plays very badly out of tune in five sharps. So an Ab tuba would make playing Bydlo use the same fingering pattern as C minor on a CC tuba (a G# tuba — eight sharps — playing in G# minor — five sharps). In theory, it would play using an easy fingering pattern that normally plays in tune with good response, so even if the horn was a genuine bowzer it ought to play in that key okay if the open horn is reasonably well in tune with itself.
If I manage to crank all this kooky crap out I will become a sort of incarnation of Harv, I think…
The Getzen could not be cut short enough to put it into Ab without using an overly-large-bore valve section. It will stay in G so I can use valves that will make sense. I have thought to lower it to F and use .689" King pistons, which might work well. In Ab that would end up having valves that are larger than .750" — I'm too stupid to work that out into a working horn, heh, heh…
My desire to do this is to put an instrument in the tenor or bass tuba range that is as close as possible to G#/Ab minor. A CC tuba plays well in A, D, G, and C minor, so those fingering patterns in relation to the "home key" of the horn would make the chances of a homemade instrument being reasonably in tune and easily correctable if it is not. Building a Bb euphonium from scratch using and bell and tubing intended for something else would likely net a horn that plays very badly out of tune in five sharps. So an Ab tuba would make playing Bydlo use the same fingering pattern as C minor on a CC tuba (a G# tuba — eight sharps — playing in G# minor — five sharps). In theory, it would play using an easy fingering pattern that normally plays in tune with good response, so even if the horn was a genuine bowzer it ought to play in that key okay if the open horn is reasonably well in tune with itself.
If I manage to crank all this kooky crap out I will become a sort of incarnation of Harv, I think…
- These users thanked the author the elephant for the post:
- arpthark (Tue Oct 11, 2022 12:31 pm)

-
- Posts: 1432
- Joined: Thu Aug 13, 2020 10:39 pm
- Location: SoCal
- Has thanked: 1553 times
- Been thanked: 467 times
Re: Holton 345 Redux
I think it is great what Wade has done. I am amazed and jealous of his perseverance. I wish I was half as persistent and detail oriented!
- These users thanked the author York-aholic for the post (total 2):
- arpthark (Tue Oct 11, 2022 12:50 pm) • the elephant (Tue Oct 11, 2022 1:20 pm)
Some old Yorks, Martins, and perhaps a King rotary valved CC
- arpthark
- Posts: 3899
- Joined: Mon Aug 24, 2020 4:25 pm
- Location: Southeastern Connecticut
- Has thanked: 951 times
- Been thanked: 1067 times
- Contact:
Re: Holton 345 Redux
As an aspiring shade tree tuba mechanic, Wade's incredibly meticulous descriptions and high-quality photos are one of my favorite parts of this website. I can waste a good hour of my lunch break going through everything!
- These users thanked the author arpthark for the post:
- the elephant (Tue Oct 11, 2022 1:21 pm)
Blake
Bean Hill Brass
Bean Hill Brass
- the elephant
- Posts: 3378
- Joined: Thu Aug 13, 2020 8:39 am
- Location: 404 - Not Found
- Has thanked: 1896 times
- Been thanked: 1335 times
Re: Holton 345 Redux
***
I'm an idiot. I posted all this in the wrong thread. Moving it to the Kurath thread now…
***
I'm an idiot. I posted all this in the wrong thread. Moving it to the Kurath thread now…

***
Last edited by the elephant on Thu Oct 20, 2022 10:47 pm, edited 1 time in total.
- These users thanked the author the elephant for the post:
- bloke (Wed Oct 19, 2022 5:41 pm)

- bloke
- Mid South Music
- Posts: 19285
- Joined: Thu Aug 13, 2020 8:55 am
- Location: western Tennessee - near Memphis
- Has thanked: 3841 times
- Been thanked: 4086 times
Re: Holton 345 Redux
wow...
You go to a whole bunch more trouble than I do...
I look around and find stuff that has the same radius/curvature as individual bends, and just bend around those things.
I guess that's why I consider myself "incredibly lucky" at doing it...because - rather than actually having a plan and a custom jig, via what you've done - I "freestyle".
You go to a whole bunch more trouble than I do...
I look around and find stuff that has the same radius/curvature as individual bends, and just bend around those things.
I guess that's why I consider myself "incredibly lucky" at doing it...because - rather than actually having a plan and a custom jig, via what you've done - I "freestyle".
- the elephant
- Posts: 3378
- Joined: Thu Aug 13, 2020 8:39 am
- Location: 404 - Not Found
- Has thanked: 1896 times
- Been thanked: 1335 times
Re: Holton 345 Redux
I usually do, too. But that netted me a FUBARed leadpipe. Sometimes we lazy guys have to dig in and take the time.
Currently, the $50 minimum order and the $30 lowest-price shipping means that one of these pipes actually cost me $80. This is the second pipe, so it is costing me $160. Therefore, I'm taking great pains to avoid making this leadpipe project cost me $240…

Currently, the $50 minimum order and the $30 lowest-price shipping means that one of these pipes actually cost me $80. This is the second pipe, so it is costing me $160. Therefore, I'm taking great pains to avoid making this leadpipe project cost me $240…

- These users thanked the author the elephant for the post:
- York-aholic (Wed Oct 19, 2022 10:38 pm)

-
- Posts: 1432
- Joined: Thu Aug 13, 2020 10:39 pm
- Location: SoCal
- Has thanked: 1553 times
- Been thanked: 467 times
Re: Holton 345 Redux
In boat building, when bending wood (steam ending solid wood or bending a stacked lamination) they use a jig like you did. Rather than slots for hose clamps, they drill bigger holes (2” maybe) and use C clamps or F clamps. Similar concept. Nicely done Mr. Elephant.
- These users thanked the author York-aholic for the post:
- the elephant (Thu Oct 20, 2022 6:18 am)
Some old Yorks, Martins, and perhaps a King rotary valved CC
- LargeTuba
- Posts: 777
- Joined: Thu Aug 13, 2020 11:08 am
- Has thanked: 97 times
- Been thanked: 136 times
Re: Holton 345 Redux
I don't know if you've said this before, but have you measured how long the bugle is? Id be curious to know how close is it to 16 feet, and how much shorter it is compared to a 345 BBb.
Pt-6P, Holton 345 CC, 45slp
- the elephant
- Posts: 3378
- Joined: Thu Aug 13, 2020 8:39 am
- Location: 404 - Not Found
- Has thanked: 1896 times
- Been thanked: 1335 times
Re: Holton 345 Redux
Okay, this may be the last post about this tuba save for final photos after it has been fully cleaned up and (possibly) refinished with lacquer or plating — and those updates are maybe years away.
I made a new leadpipe that really screwed with the horn's distinct playing characteristics of the past. Honestly, I disliked it enough that I was considering making another one. But I had just gotten used to how weird things were, telling myself that these big horns have issues that are very hard to correct due to their extreme taper rate and how and where things are bent, etc.
Excuses, excuses…
I was wrong. While this will never be a perfect tuba, I think I have managed to dial it in enough that I like it as much as my Mirafone 186, which is not a great example of that model, but is *very* good, and is tailored to how I play. In short — I love my 186. And now I can say the same for this Holton beastie: I love it.
History of he leadpipe:
• Rusk used an 11" long section of a french horn bell tail. It needed to taper from 15mm to 19mm in less than a foot, so he solved that by using the horn part. This means the leadpipe started expanding as soon as it left the receiver. Then he had an 18mm rotary valve stuck on the end of that, and the gap was filled with so much solder that it created an annulus within the entry and exit ports of the valve that reduced the bore to about 17mm. I am not exaggerating about this. It was a freaking mess. Because of the 1st slide design, the 5th valve could not be installed directly to the 1st valve knuckle. So there was a 30mm stand-off tube between the rotor and piston cases. This also did not fit all that well, but it was passable.
• I bent a generic taper Allied leadpipe to replace the horn bell section. I deleted the 5th valve altogether and played the horn as a four-banger for about a year. EVERYTHING was improved with my leadpipe, so that, with its visible flaws, I had absolutely no desire to "fix" it. I used this leadpipe for years.
• The final design and installation of the removable valve machine caused the whole thing to have to be shifted down and away from where it had lived for many years. We are talking about probably 10mm over and maybe 5mm down, but it was enough that my leadpipe no longer could be used. I also had been reading a lot of Joe's ideas about a tighter leadpipe on big horns like this, and him talking about the first six inches or so being choked down a little to stabilize the low range. (I cannot remember what this was in reference to, but it may have been something he was fooling around with on "Fat Bastard". Whatever. It made a lot of sense, and this Holton suffered from a very challenging low range with Rusk's funkified leadpipe, and I improved it a lot with my smaller replacement. So I decided the new leadpipe would 1.) correct my field of vision, and 2.) be tighter in the first six inches. The shape was an out-of-the-park homerun for me. However, everything changed with the skinnier leadpipe. My main gripe was that I could no longer use my beloved Sellmansberger Solo on this tuba; it just didn't work anymore.
So I switched to a stupid-large bucket mouthpiece (that secretly I love to death, heh, heh…) and that fixed a lot of the issues introduced by this "failed" leadpipe. I would just use this mouthpiece and practice until I was more familiar with this setup. I could bend another leadpipe in the future. It was perfect, but it was too skinny.
Or so I thought.
This past weekend I decided to use the Holton for this week's Masterworks Series concert. I have to use a mute so I decided to play all my daily drills with the mute in and tuner on, use drone pitches, etc. — the whole ball of wax. I like muted practice as it helps me work through my personal air issues, but I had not done any since the pandemic started. This was a good decision, as I had so many issues with muted intonation that I started doing all this work senza sordino, and that was quite educational.
I had altered the entire scale of the tuba with my rather severe leadpipe alterations. I was still humoring everything as this horn demands, and I eventually realized that none of this had to be done anymore. After hours of working on one etude in 24 settings (low and high octaves in all 12 keys), I worked out many of the intonation issues.
Then I discovered that all of my pistons leak.
Great. Just great.
I had suspected that the 2nd valve leaked for some time, as shortening the slide to make be able to lift the sagging low "B" with a slide push. I shortened that slide three times, and that same low "B" never moved, though everything else did.
I do not have much experience with dealing with leaking pistons other than just selling the horn. That is not an option, in this case, though.
So I mixed up some heavier valve oil et voila! I have a brand-new tuba!
My leadpipe was exactly what the horn needed to fix most of the response issues, and once everything shifted around to be more stable I could put slides where they *really* need to be, find useful alternates when needed, and all that sort of stuff. But then SEALING THE DANG LEAKING PISTONS fixed it all.
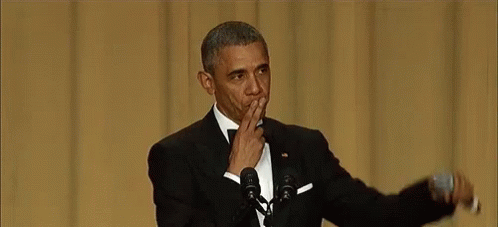
It is THAT big of a difference.
In years past I used Hetman lubes, and the piston oil is a bit more viscous than the straight lamp oil I am now using. I agree with Joe on this stuff: it is great, and it is cheap, and it makes a great base for various homebrew concoctions. It cleans, too.
And I think that is where the leaks began. My old valves were leaking before I got this tuba, and I suspect that lime and other crap had been sealing up things in every valve except for 2nd. Switching to lamp oil cleaned all that stuff off, making the horn leak more and causing the intonation to become noticeably "off" over time. This was a great thing, as it allowed me to find a hidden issue and finally address it. This tuba leaked all over the place when I got it. I have addressed all of this simply by soldering joints well and then leak-testing each one as I go, but this last set of leaks really surprised me.
So the cleaning power of lamp oil is very real, and it is a good thing. Now I have a 50/50 mix of lamp oil and 3-in-One that does not hamper action and causes the intonation to really line up well.
The lamp oil alone evaporates terribly fast, so I have to oil my valves every day, and on long days I have to oil them twice. The 3-in-One thickens it and also slows evaporation. So far it has not become gummy, but I imagine that as the lamp oil part evaporates I will have to use less of the 3-in-One in the mix. So I ginned up three bottles that I will test over time. I think the heavier oil I have been using over the weekend applied a nice base of the 3-in-One, but I will want to use thinner stuff after the first week or so. I really don't know.
So the new leadpipe and a much heavier oil seem to have turned this tuba into a genuine player!
Now, the upper 1st, 3rd, and 4th slides are much farther out than in the past. I do not want to have to remove and replace all these outer tubes (and all the connected braces) to extend them, so I will go the other route and remove spacers and install longer inner legs, and use much longer ferrules to make things look nicer.
Here are where my upper slides used to be…

Here are where they are, now…

The biggest difference is in 1st, and it is near all the way out now. None of these have to be moved in much father than this ever, with this leadpipe and mouthpiece. I really like this idiotic mouthpiece, so I will probably stay with it. So I guess this is where the slide will live for the most part from now on. So I can make longer slides and not have to hack up the valve section at all.
Nice!
I have never been happier with this tuba. It really is as good as the Miraphone now. All the wonky notes are fixed.
Of course, at some point, I will want to have a top-notch valve rebuild done, but the heavier oil works so well that I can probably put that off for several years.
This tuba plays so much better than it did when I got it back in 2007.
I am glad I finally pulled my head out and realized the valves were leaking. I really like lamp oil, now. It helps you uncover issues so that they can be fixed. And it is a great, cheap lubricant. Thanks for all that preaching, Joe.
N.B. — The Kurath has the very same issue: the 2nd valve leaks; perhaps all of them leak. I will try this same oil mixture on it tomorrow and do the same musical work with it to see how things are affected, and then see how it works in the quintet on Friday morning.
I made a new leadpipe that really screwed with the horn's distinct playing characteristics of the past. Honestly, I disliked it enough that I was considering making another one. But I had just gotten used to how weird things were, telling myself that these big horns have issues that are very hard to correct due to their extreme taper rate and how and where things are bent, etc.
Excuses, excuses…
I was wrong. While this will never be a perfect tuba, I think I have managed to dial it in enough that I like it as much as my Mirafone 186, which is not a great example of that model, but is *very* good, and is tailored to how I play. In short — I love my 186. And now I can say the same for this Holton beastie: I love it.
History of he leadpipe:
• Rusk used an 11" long section of a french horn bell tail. It needed to taper from 15mm to 19mm in less than a foot, so he solved that by using the horn part. This means the leadpipe started expanding as soon as it left the receiver. Then he had an 18mm rotary valve stuck on the end of that, and the gap was filled with so much solder that it created an annulus within the entry and exit ports of the valve that reduced the bore to about 17mm. I am not exaggerating about this. It was a freaking mess. Because of the 1st slide design, the 5th valve could not be installed directly to the 1st valve knuckle. So there was a 30mm stand-off tube between the rotor and piston cases. This also did not fit all that well, but it was passable.
• I bent a generic taper Allied leadpipe to replace the horn bell section. I deleted the 5th valve altogether and played the horn as a four-banger for about a year. EVERYTHING was improved with my leadpipe, so that, with its visible flaws, I had absolutely no desire to "fix" it. I used this leadpipe for years.
• The final design and installation of the removable valve machine caused the whole thing to have to be shifted down and away from where it had lived for many years. We are talking about probably 10mm over and maybe 5mm down, but it was enough that my leadpipe no longer could be used. I also had been reading a lot of Joe's ideas about a tighter leadpipe on big horns like this, and him talking about the first six inches or so being choked down a little to stabilize the low range. (I cannot remember what this was in reference to, but it may have been something he was fooling around with on "Fat Bastard". Whatever. It made a lot of sense, and this Holton suffered from a very challenging low range with Rusk's funkified leadpipe, and I improved it a lot with my smaller replacement. So I decided the new leadpipe would 1.) correct my field of vision, and 2.) be tighter in the first six inches. The shape was an out-of-the-park homerun for me. However, everything changed with the skinnier leadpipe. My main gripe was that I could no longer use my beloved Sellmansberger Solo on this tuba; it just didn't work anymore.
So I switched to a stupid-large bucket mouthpiece (that secretly I love to death, heh, heh…) and that fixed a lot of the issues introduced by this "failed" leadpipe. I would just use this mouthpiece and practice until I was more familiar with this setup. I could bend another leadpipe in the future. It was perfect, but it was too skinny.
Or so I thought.
This past weekend I decided to use the Holton for this week's Masterworks Series concert. I have to use a mute so I decided to play all my daily drills with the mute in and tuner on, use drone pitches, etc. — the whole ball of wax. I like muted practice as it helps me work through my personal air issues, but I had not done any since the pandemic started. This was a good decision, as I had so many issues with muted intonation that I started doing all this work senza sordino, and that was quite educational.
I had altered the entire scale of the tuba with my rather severe leadpipe alterations. I was still humoring everything as this horn demands, and I eventually realized that none of this had to be done anymore. After hours of working on one etude in 24 settings (low and high octaves in all 12 keys), I worked out many of the intonation issues.
Then I discovered that all of my pistons leak.
Great. Just great.
I had suspected that the 2nd valve leaked for some time, as shortening the slide to make be able to lift the sagging low "B" with a slide push. I shortened that slide three times, and that same low "B" never moved, though everything else did.
I do not have much experience with dealing with leaking pistons other than just selling the horn. That is not an option, in this case, though.
So I mixed up some heavier valve oil et voila! I have a brand-new tuba!
My leadpipe was exactly what the horn needed to fix most of the response issues, and once everything shifted around to be more stable I could put slides where they *really* need to be, find useful alternates when needed, and all that sort of stuff. But then SEALING THE DANG LEAKING PISTONS fixed it all.
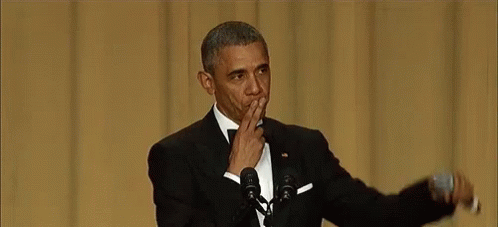
It is THAT big of a difference.
In years past I used Hetman lubes, and the piston oil is a bit more viscous than the straight lamp oil I am now using. I agree with Joe on this stuff: it is great, and it is cheap, and it makes a great base for various homebrew concoctions. It cleans, too.
And I think that is where the leaks began. My old valves were leaking before I got this tuba, and I suspect that lime and other crap had been sealing up things in every valve except for 2nd. Switching to lamp oil cleaned all that stuff off, making the horn leak more and causing the intonation to become noticeably "off" over time. This was a great thing, as it allowed me to find a hidden issue and finally address it. This tuba leaked all over the place when I got it. I have addressed all of this simply by soldering joints well and then leak-testing each one as I go, but this last set of leaks really surprised me.
So the cleaning power of lamp oil is very real, and it is a good thing. Now I have a 50/50 mix of lamp oil and 3-in-One that does not hamper action and causes the intonation to really line up well.
The lamp oil alone evaporates terribly fast, so I have to oil my valves every day, and on long days I have to oil them twice. The 3-in-One thickens it and also slows evaporation. So far it has not become gummy, but I imagine that as the lamp oil part evaporates I will have to use less of the 3-in-One in the mix. So I ginned up three bottles that I will test over time. I think the heavier oil I have been using over the weekend applied a nice base of the 3-in-One, but I will want to use thinner stuff after the first week or so. I really don't know.
So the new leadpipe and a much heavier oil seem to have turned this tuba into a genuine player!
Now, the upper 1st, 3rd, and 4th slides are much farther out than in the past. I do not want to have to remove and replace all these outer tubes (and all the connected braces) to extend them, so I will go the other route and remove spacers and install longer inner legs, and use much longer ferrules to make things look nicer.
Here are where my upper slides used to be…

Here are where they are, now…

The biggest difference is in 1st, and it is near all the way out now. None of these have to be moved in much father than this ever, with this leadpipe and mouthpiece. I really like this idiotic mouthpiece, so I will probably stay with it. So I guess this is where the slide will live for the most part from now on. So I can make longer slides and not have to hack up the valve section at all.
Nice!
I have never been happier with this tuba. It really is as good as the Miraphone now. All the wonky notes are fixed.
Of course, at some point, I will want to have a top-notch valve rebuild done, but the heavier oil works so well that I can probably put that off for several years.
This tuba plays so much better than it did when I got it back in 2007.
I am glad I finally pulled my head out and realized the valves were leaking. I really like lamp oil, now. It helps you uncover issues so that they can be fixed. And it is a great, cheap lubricant. Thanks for all that preaching, Joe.
N.B. — The Kurath has the very same issue: the 2nd valve leaks; perhaps all of them leak. I will try this same oil mixture on it tomorrow and do the same musical work with it to see how things are affected, and then see how it works in the quintet on Friday morning.
