
Silver plating
Forum rules
This section is for posts that are directly related to performance, performers, or equipment. Social issues are allowed, as long as they are directly related to those categories. If you see a post that you cannot respond to with respect and courtesy, we ask that you do not respond at all.
This section is for posts that are directly related to performance, performers, or equipment. Social issues are allowed, as long as they are directly related to those categories. If you see a post that you cannot respond to with respect and courtesy, we ask that you do not respond at all.
-
- Posts: 1045
- Joined: Thu Aug 13, 2020 8:41 am
- Has thanked: 41 times
- Been thanked: 80 times
Re: Silver plating
By that logic of air stream and lip vibrations being the sole cause of resonance and sound and (not) metals, a Mack Brass versus a 1960's Alex wouldn't matter then and everyone should be buying the least expensive instruments with the thinnest cheapest metals because there's no difference between metals made and assembled in China versus Germany and they play no role in sound production? I can't believe everyone got this wrong over the years. My precision bass is actually a Japanese made "stencil" of a Fender from the "lawsuit" era. Every curve is identical. Head stock reads "Ventura" but you would never know the difference. Put up against Fenders of the same era, it plays and sounds better than most of them. I wonder if they tried styrofoam instead of Ash bodies and maybe vinyl fretboards instead of Rosewood? Some bassists would still argue "It's all in the fingers". 

06' Miraphone 187-4U
- bloke
- Mid South Music
- Posts: 19413
- Joined: Thu Aug 13, 2020 8:55 am
- Location: western Tennessee - near Memphis
- Has thanked: 3871 times
- Been thanked: 4137 times
Re: Silver plating
Gronitz produced some of the thinnest tubas I've ever personally encountered.
I bought one - the 6/4 model, pitched in C ...It wasn't cheap, and nor was it cheaply-made.
I enjoyed carrying it, as it weighed no more than my F-tuba, but I neither credit nor discredit its thin construction with its excellent sound and excellent playing characteristics. Rather, I credit the interior shape of it. I sold it to the tuba player in the Montreal Symphony, who was one of my students.
That instrument is also silver plated, but I also offer that feature no credit, regarding how well that instrument plays.
That very thin instrument can be heard on this recording (tracks #'s 4, 5, & 6)
https://music.apple.com/us/album/the-ro ... /168285438
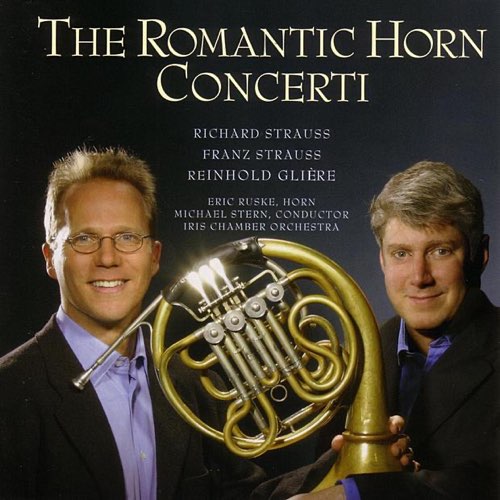
How's the new fb tubas-for-sale page going?
I bought one - the 6/4 model, pitched in C ...It wasn't cheap, and nor was it cheaply-made.
I enjoyed carrying it, as it weighed no more than my F-tuba, but I neither credit nor discredit its thin construction with its excellent sound and excellent playing characteristics. Rather, I credit the interior shape of it. I sold it to the tuba player in the Montreal Symphony, who was one of my students.
That instrument is also silver plated, but I also offer that feature no credit, regarding how well that instrument plays.
That very thin instrument can be heard on this recording (tracks #'s 4, 5, & 6)
https://music.apple.com/us/album/the-ro ... /168285438
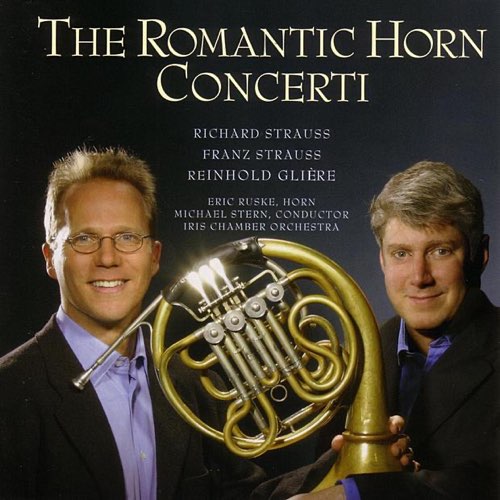
How's the new fb tubas-for-sale page going?

-
- Posts: 1045
- Joined: Thu Aug 13, 2020 8:41 am
- Has thanked: 41 times
- Been thanked: 80 times
Re: Silver plating
Yep some horns have it and some of the same lineage don't have it, just like a fine automobile built on a Friday or Monday with the exact same materials may be the one that blows a head gasket at 25k miles versus the one made the next morning may go 300k miles before it does based on who and when put it together. Now attributing the metallurgy discussion to other examples, we can compare fiberglass sousaphones with brass ones. I suppose the sound a good player like Chris Olka might produce on either one would be the exact same and if he was in the market for one he may opt for the fiberglass one since resonance has little or nothing to do with the composition of materials? Just trying to get the perspective here.I neither credit nor discredit its thin construction with its excellent sound and excellent playing characteristics.
06' Miraphone 187-4U
Re: Silver plating
I think you will get argument on that statement. Reynold Schilke never put lacquer on one of his horns because he said it would not resonate. He plated his instruments in both silver and top it with gold or other metals when ordered. I have not ever seen a nickle plated instrument but weren't the old bugles chrome plated?KingTuba1241X wrote: ↑Sat Sep 05, 2020 1:19 pm I can say whatever "plating" you decide on whether it be Silver or Nickel or...the more layers and thicker it is the less the horn resonates. I'd been looking for a clear silver horn for awhile and finally found one. Satin looks nice, it definitely deadens the sound. It's been discussed ad nausea on the old TN site and maybe the archive still exists somewhere.
The 4X silver plate on an instrument is still only microns thick. You can plate without concern for "dulling" the sound. Mr. Schilke thought it made no difference. Other people have their own ideas. Interestingly, in the mid-80s a North Texas doctoral candidate ran a test with Miraphone 188 tubas and a focus group of music majors. He had 2 new lacquered 188s, two silver plated 188s, one new and used... and one raw brass used 188.
The results were astounding. The audience found more difference between the two new lacquered 188s that between lacquer-silver or raw brass-silver or raw brass-lacquer.
I don't know what Mr. Schilke would have said about that. My thought is that the finish makes less difference in the horn than the way it is put together.
-
- Posts: 1045
- Joined: Thu Aug 13, 2020 8:41 am
- Has thanked: 41 times
- Been thanked: 80 times
Re: Silver plating
Was a Satin silver horn one of those two "silver" plated ones they used for the test? I can tell you by the process it takes to create such finish it will make a difference in overall resonance. I'm not saying the horn makes no sound at all or even drastically reduces resonance, simply that it could and will alter the "pop" of the horn so to speak. Have you ever seen the effects of sound deadening panels or insulation in cars along the firewall and in the doors and how they reduce engine, wind and road noise from penetrating the metal exterior? A lot of fine expensive automobiles (and some mid range ones as well these days) have used it for decades. Exhaust guys also heat wrap/noise reducing down pipes and muffler systems to deaden excessive noise and heat as well. If applied to brass tubing in the form of sand blasting or the processes for such a satin finish one could expect a similar outcome. I've also done a test like they did in North Texas, with 4 of the same instruments in different finishes and 3 different players testing them. 2 lacquer (one peeling badly), 3 silver (2 of them being Satin silver and in proper working order) we all found the satin ones to have less overtones and a noticeably different (not positive) timbre and resonance. The standard silver was very good and the lacquered ones seemed the best (I am partial to Silver and wanted different results but couldn't deny the horn with even the least amount of lacquer felt more alive in all 3 player's hands). YMMV though.Alex C wrote: ↑Mon Sep 07, 2020 9:50 amI think you will get argument on that statement. Reynold Schilke never put lacquer on one of his horns because he said it would not resonate. He plated his instruments in both silver and top it with gold or other metals when ordered. I have not ever seen a nickle plated instrument but weren't the old bugles chrome plated?KingTuba1241X wrote: ↑Sat Sep 05, 2020 1:19 pm I can say whatever "plating" you decide on whether it be Silver or Nickel or...the more layers and thicker it is the less the horn resonates. I'd been looking for a clear silver horn for awhile and finally found one. Satin looks nice, it definitely deadens the sound. It's been discussed ad nausea on the old TN site and maybe the archive still exists somewhere.
The 4X silver plate on an instrument is still only microns thick. You can plate without concern for "dulling" the sound. Mr. Schilke thought it made no difference. Other people have their own ideas. Interestingly, in the mid-80s a North Texas doctoral candidate ran a test with Miraphone 188 tubas and a focus group of music majors. He had 2 new lacquered 188s, two silver plated 188s, one new and used... and one raw brass used 188.
The results were astounding. The audience found more difference between the two new lacquered 188s that between lacquer-silver or raw brass-silver or raw brass-lacquer.
I don't know what Mr. Schilke would have said about that. My thought is that the finish makes less difference in the horn than the way it is put together.
06' Miraphone 187-4U
- bloke
- Mid South Music
- Posts: 19413
- Joined: Thu Aug 13, 2020 8:55 am
- Location: western Tennessee - near Memphis
- Has thanked: 3871 times
- Been thanked: 4137 times
Re: Silver plating
again:
Just because someone has some remarkable abilities (performing, constructing, repairing, whatever) doesn't mean that every single bit of their perceiving is going to accurate.
I look askance at statements/beliefs whereby a thinner-than-the-thinnest-plastic-wrap coating of a clear paint ("lacquer") is going to cause some effect that will override (OK: considering the name mentioned) the difference in sonority between a size 6A4A "Bill Chase Model" trumpet mouthpiece and a size 24 trumpet mouthpiece.
Further, lacquer thick enough to possibly (????) actually begin to make some barely-noticeable difference in resonance would need to be thick enough to last through two or three "rough use" players' lifetimes, and no applied lacquer - that I've ever seen on a brass instrument - is that thick.
My strong (and I'm the guy sitting behind the table with the "CHANGE MY MIND" sign) believe is that two instruments that theoretically could be made absolutely identical (which is currently impossible) - whereby one of them is fabricated of .5mm brass and the other is fabricated of .6mm brass, would SOUND the same, yet (OK...) FEEL different in a player's hands...
Moreover, it is my very strong belief that tactile features are HUGE influencers of perceptions which are believed - by perceivers - to be aural.
>> Some of us will remember a thing sold a couple of decades ago called a "Pocket Rocket", whereby musicians (vocalists and instrumentalists...but MOSTLY trumpet players bought them) whereby bits of various types of wood or metal were sold for musicians to place (yes) in their shirt or pants pocket...to affect the resonance of their voices or of their instruments.
Just because someone has some remarkable abilities (performing, constructing, repairing, whatever) doesn't mean that every single bit of their perceiving is going to accurate.
I look askance at statements/beliefs whereby a thinner-than-the-thinnest-plastic-wrap coating of a clear paint ("lacquer") is going to cause some effect that will override (OK: considering the name mentioned) the difference in sonority between a size 6A4A "Bill Chase Model" trumpet mouthpiece and a size 24 trumpet mouthpiece.
Further, lacquer thick enough to possibly (????) actually begin to make some barely-noticeable difference in resonance would need to be thick enough to last through two or three "rough use" players' lifetimes, and no applied lacquer - that I've ever seen on a brass instrument - is that thick.
My strong (and I'm the guy sitting behind the table with the "CHANGE MY MIND" sign) believe is that two instruments that theoretically could be made absolutely identical (which is currently impossible) - whereby one of them is fabricated of .5mm brass and the other is fabricated of .6mm brass, would SOUND the same, yet (OK...) FEEL different in a player's hands...
Moreover, it is my very strong belief that tactile features are HUGE influencers of perceptions which are believed - by perceivers - to be aural.
>> Some of us will remember a thing sold a couple of decades ago called a "Pocket Rocket", whereby musicians (vocalists and instrumentalists...but MOSTLY trumpet players bought them) whereby bits of various types of wood or metal were sold for musicians to place (yes) in their shirt or pants pocket...to affect the resonance of their voices or of their instruments.

- matt g
- Posts: 2583
- Joined: Thu Aug 13, 2020 10:37 am
- Location: Southeastern New England
- Has thanked: 263 times
- Been thanked: 555 times
Re: Silver plating
@bloke, the “human in the loop” is certainly an important aspect of all of this.
It would be fun to haul out that trumpet playing robot and have it play a bunch of different variations on a Bb trumpet. Plating, bracing, thickness, weighted caps, all of it.
Put it behind a curtain and let a lot of people listen and judge in isolation. Bring a spectrum analyzer along for digital data capture and analysis.
Assuming these horns were built with at least the same level of care, knowing precision will vary, it would be interesting to see the comparison.
My gut tells me that differences will be minimal, especially in the acoustic far field.
But, the horn providing different (near field) feedback to a human player can make significant differences in playing.
With all of that being said, I don’t care for silver horns because they tarnish and start to take on an “onion-like” smell after a while.
It would be fun to haul out that trumpet playing robot and have it play a bunch of different variations on a Bb trumpet. Plating, bracing, thickness, weighted caps, all of it.
Put it behind a curtain and let a lot of people listen and judge in isolation. Bring a spectrum analyzer along for digital data capture and analysis.
Assuming these horns were built with at least the same level of care, knowing precision will vary, it would be interesting to see the comparison.
My gut tells me that differences will be minimal, especially in the acoustic far field.
But, the horn providing different (near field) feedback to a human player can make significant differences in playing.
With all of that being said, I don’t care for silver horns because they tarnish and start to take on an “onion-like” smell after a while.
Dillon/Walters CC (sold)
Meinl-Weston 2165 (sold)
Meinl-Weston 2165 (sold)
- bloke
- Mid South Music
- Posts: 19413
- Joined: Thu Aug 13, 2020 8:55 am
- Location: western Tennessee - near Memphis
- Has thanked: 3871 times
- Been thanked: 4137 times
Re: Silver plating
yes...but there would still be a human factor: the judgingmatt g wrote: ↑Mon Sep 07, 2020 10:55 am @bloke, the “human in the loop” is certainly an important aspect of all of this.
It would be fun to haul out that trumpet playing robot and have it play a bunch of different variations on a Bb trumpet. Plating, bracing, thickness, weighted caps, all of it.
Put it behind a curtain and let a lot of people listen and judge in isolation. Bring a spectrum analyzer along for digital data capture and analysis.
Assuming these horns were built with at least the same level of care, knowing precision will vary, it would be interesting to see the comparison.
My gut tells me that differences will be minimal, especially in the acoustic far field.
But, the horn providing different (near field) feedback to a human player can make significant differences in playing.
With all of that being said, I don’t care for silver horns because they tarnish and start to take on an “onion-like” smell after a while.

onion...hmm...To me, tarnished silver smells like sulfur. I'll consider your "onion" olfactory perception, the next time I'm exposed to that.
- matt g
- Posts: 2583
- Joined: Thu Aug 13, 2020 10:37 am
- Location: Southeastern New England
- Has thanked: 263 times
- Been thanked: 555 times
Re: Silver plating
@bloke, that’s the little details of behind the curtain and voting in isolation. We all know how silly people can be. If acting alone and anonymously without knowledge of what is being tooted on, you’ll get an approximation if honesty.
Dillon/Walters CC (sold)
Meinl-Weston 2165 (sold)
Meinl-Weston 2165 (sold)
- matt g
- Posts: 2583
- Joined: Thu Aug 13, 2020 10:37 am
- Location: Southeastern New England
- Has thanked: 263 times
- Been thanked: 555 times
Re: Silver plating
Simply regarding the physics aspect of all of this, does anyone have the calculated impedance of clear lacquer, brass, silver, etc.?
Have they compared this to air?
Assuming there is refraction in the boundaries of the waveguide (tubing), what frequencies should we be concerned with? Hint: there’s a direct correlation between the thickness of the medium and wavelength. Consider which frequencies have a small enough wavelength to travel in the tubing walls without evanescent decay.
Most of the math and models in my head points to very little difference (essentially zero) in frequencies of interest to humans that a tuba will generate. Again, this is in respect to long range propagation of the signal.
Sympathetic resonance is real, but rarely heard if the tuba is in good order. Loose braces will rattle loudly because you know have a new opportunity for mechanical noise to be made. Assuming that’s all handled, there certainly can be horns that “feel alive” in the hands that bring a welcome response.
Have they compared this to air?
Assuming there is refraction in the boundaries of the waveguide (tubing), what frequencies should we be concerned with? Hint: there’s a direct correlation between the thickness of the medium and wavelength. Consider which frequencies have a small enough wavelength to travel in the tubing walls without evanescent decay.
Most of the math and models in my head points to very little difference (essentially zero) in frequencies of interest to humans that a tuba will generate. Again, this is in respect to long range propagation of the signal.
Sympathetic resonance is real, but rarely heard if the tuba is in good order. Loose braces will rattle loudly because you know have a new opportunity for mechanical noise to be made. Assuming that’s all handled, there certainly can be horns that “feel alive” in the hands that bring a welcome response.
Dillon/Walters CC (sold)
Meinl-Weston 2165 (sold)
Meinl-Weston 2165 (sold)
- bloke
- Mid South Music
- Posts: 19413
- Joined: Thu Aug 13, 2020 8:55 am
- Location: western Tennessee - near Memphis
- Has thanked: 3871 times
- Been thanked: 4137 times
Re: Silver plating
For that (those) matter(s), who has EVER experimented with various levels of HUMIDITY in the air, and how THAT affects wind instrument resonance and performance efficiency...?? anyone...??
-
- Posts: 1045
- Joined: Thu Aug 13, 2020 8:41 am
- Has thanked: 41 times
- Been thanked: 80 times
Re: Silver plating
So you don’t believe a fiberglass horn has less resonance and feedback (to the player or listener) than a brass one? Going by the opinions thus far expressed i wouldn’t expect there to be any difference or “Because George was hungover last Monday morning and he didn’t solder something up correctly therefore it plays worse than Tuesday morning’s batch when he had a better nights sleep”. Lovely thing about opinions is they are always just that.
06' Miraphone 187-4U
- matt g
- Posts: 2583
- Joined: Thu Aug 13, 2020 10:37 am
- Location: Southeastern New England
- Has thanked: 263 times
- Been thanked: 555 times
Re: Silver plating
Fiberglass is a good question.KingTuba1241X wrote: ↑Mon Sep 07, 2020 11:19 am So you don’t believe a fiberglass horn has less resonance and feedback (to the player or listener) than a brass one? Going by the opinions thus far expressed i wouldn’t expect there to be any difference or “Because George was hungover last Monday morning and he didn’t solder something up correctly therefore it plays worse than Tuesday morning’s batch when he had a better nights sleep”. Lovely thing about opinions is they are always just that.
I think that you now have:
-a much thicker wall, i.e. much more dead externally
-a porous wall that has mixed properties (there is air trapped in the walls) that probably does some weird things
-a different “roughness” to the surface
-introduction of joints that tend to leak
Having said this, I played a 36K at WDW (owned and maintained by them) that sounded great from about 20 feet away.
Dillon/Walters CC (sold)
Meinl-Weston 2165 (sold)
Meinl-Weston 2165 (sold)
-
- Posts: 1045
- Joined: Thu Aug 13, 2020 8:41 am
- Has thanked: 41 times
- Been thanked: 80 times
Re: Silver plating
Well good thing the valve and slide section is brass. That's cool you played at WDW, was that a main gig for you?
06' Miraphone 187-4U
- matt g
- Posts: 2583
- Joined: Thu Aug 13, 2020 10:37 am
- Location: Southeastern New England
- Has thanked: 263 times
- Been thanked: 555 times
Re: Silver plating
I was just a college musician.KingTuba1241X wrote: ↑Mon Sep 07, 2020 12:13 pm Well good thing the valve and slide section is brass. That's cool you played at WDW, was that a main gig for you?
I’m guessing that the tubing that’s left as brass is to keep construction costs down along with repair and service needs in mind. Interchangeable parts and all.
There was a theory floated back in the days of internet tuba chat enlightenment about silver tubas playing better simply because all of the joints were sealed well and insured of such because of the plating process. I have no idea of the merit of that argument, but it could be interesting.
Lacquer, being sprayed on or deposited via electrostatic means, wouldn’t fill in nooks and crannies like the submersion process for plating would.
Dillon/Walters CC (sold)
Meinl-Weston 2165 (sold)
Meinl-Weston 2165 (sold)
- matt g
- Posts: 2583
- Joined: Thu Aug 13, 2020 10:37 am
- Location: Southeastern New England
- Has thanked: 263 times
- Been thanked: 555 times
Re: Silver plating
An aside:
I remember playing a Jupiter sousaphone that was fiberglass body, and silver plated bell and valve block.
No idea what was going on with that, but it was terrible.
I remember playing a Jupiter sousaphone that was fiberglass body, and silver plated bell and valve block.
No idea what was going on with that, but it was terrible.
Dillon/Walters CC (sold)
Meinl-Weston 2165 (sold)
Meinl-Weston 2165 (sold)
-
- Posts: 103
- Joined: Wed Aug 26, 2020 1:09 pm
- Has thanked: 8 times
- Been thanked: 6 times
- bloke
- Mid South Music
- Posts: 19413
- Joined: Thu Aug 13, 2020 8:55 am
- Location: western Tennessee - near Memphis
- Has thanked: 3871 times
- Been thanked: 4137 times
Re: Silver plating
LOL...
“fiberglass”...”silver”...
bloke “JUPITER !!!!”

Last edited by bloke on Tue Sep 08, 2020 5:59 am, edited 1 time in total.
-
- Posts: 1045
- Joined: Thu Aug 13, 2020 8:41 am
- Has thanked: 41 times
- Been thanked: 80 times
Re: Silver plating
Filter what you can and find what works and sounds good to you, it's your time and money at the end of the day.joshealejo wrote: ↑Mon Sep 07, 2020 8:59 pm Thank you so much for the responses! It is more clear now!
06' Miraphone 187-4U
- bloke
- Mid South Music
- Posts: 19413
- Joined: Thu Aug 13, 2020 8:55 am
- Location: western Tennessee - near Memphis
- Has thanked: 3871 times
- Been thanked: 4137 times
Re: Silver plating
Either sprayed-on lacquer of silver plating can easily be buffed through (to the brass) with a buffing machine in about two or three seconds...
...so it's very unlikely that either has any easily-perceivable effect on anything sonic, as it's typically only about 10 microns thickness of this cosmetically-related material (vs. 600 microns thickness of structural material)...ie. 1:60, or about 1-1/2% of the total thickness (again, with - not the thickness of the material, but - the shape of the air column being the overwhelming factor in sonority qualities/characteristics).
"Practicing", though...WOW !!!...what an effect THAT can have !!!
Bright silver plating (as satin silver plating was more common - when silver was applied, previously, and lacquer finishes had become the rule) became popular around 1970, when Carl "Doc" Severinsen - on NBC's "Tonight Show" (who also wore wild-patterned and bright-colors cutting-edge styles of clothing) began playing a BRIGHT silver-plated Getzen-manufactured trumpet.
Of course, MANY trumpet players just HAD to have one of those, felt a bit embarrassed that (mostly) they were buying those (flashy) trumpets for vanity and "to be like Doc" purposes...so they claimed that the 10 microns of silver "affected the sound"...
...and - soon after - King (a company that actually offered SOLID silver-bell/mouthpipe trumpets as options) had to compete with Getzen (as people were buying those Getzen trumpets like CRAZY), King had (a few years earlier - actually to attempt to compete with the Schilke/Bach market) introduced their (thinner brass bell) "SILVER FLAIR" (a merely silver-PLATED) trumpet, but (with the Severinsen/Getzen craze) began heavily promoting their "Silver Flair"...
...and - at that point - the "BRIGHT SILVER" craze (with brass instruments) was "off to the races".
[ ' funny how this has NEVER caught on with French horns (as so many French horn players are hyper "affects the sound" superstitious)...with the obvious/practical reason being that post-plating factory clean-up - with silver plated French horns - is a nightmare - as is owner maintenance...with all of those inaccessible surfaces.]
That having been said, there were a couple of small manufacturers (like Schilke) that never lacquered their instruments...but (in particular) Schilke trumpets - with no silver to cover up the base metals - are fabricated of such a hodge-podge of metals, that (well...) they look "goofy" without silver unifying their appearance.
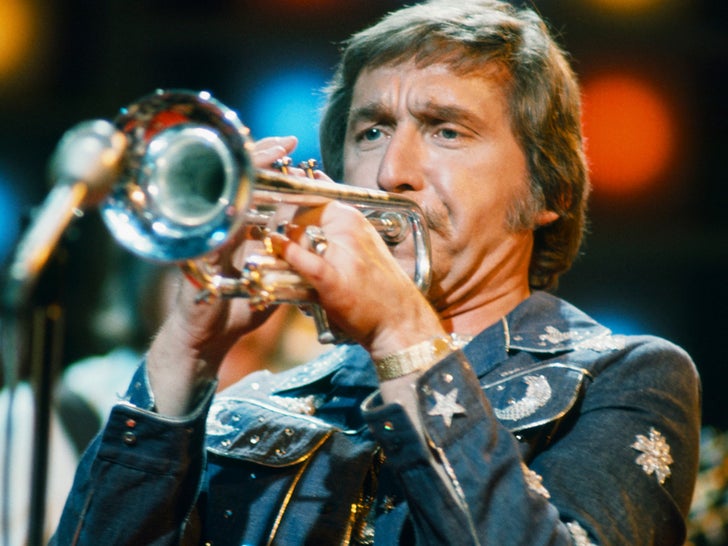
...so it's very unlikely that either has any easily-perceivable effect on anything sonic, as it's typically only about 10 microns thickness of this cosmetically-related material (vs. 600 microns thickness of structural material)...ie. 1:60, or about 1-1/2% of the total thickness (again, with - not the thickness of the material, but - the shape of the air column being the overwhelming factor in sonority qualities/characteristics).
"Practicing", though...WOW !!!...what an effect THAT can have !!!

Bright silver plating (as satin silver plating was more common - when silver was applied, previously, and lacquer finishes had become the rule) became popular around 1970, when Carl "Doc" Severinsen - on NBC's "Tonight Show" (who also wore wild-patterned and bright-colors cutting-edge styles of clothing) began playing a BRIGHT silver-plated Getzen-manufactured trumpet.
Of course, MANY trumpet players just HAD to have one of those, felt a bit embarrassed that (mostly) they were buying those (flashy) trumpets for vanity and "to be like Doc" purposes...so they claimed that the 10 microns of silver "affected the sound"...
...and - soon after - King (a company that actually offered SOLID silver-bell/mouthpipe trumpets as options) had to compete with Getzen (as people were buying those Getzen trumpets like CRAZY), King had (a few years earlier - actually to attempt to compete with the Schilke/Bach market) introduced their (thinner brass bell) "SILVER FLAIR" (a merely silver-PLATED) trumpet, but (with the Severinsen/Getzen craze) began heavily promoting their "Silver Flair"...
...and - at that point - the "BRIGHT SILVER" craze (with brass instruments) was "off to the races".

[ ' funny how this has NEVER caught on with French horns (as so many French horn players are hyper "affects the sound" superstitious)...with the obvious/practical reason being that post-plating factory clean-up - with silver plated French horns - is a nightmare - as is owner maintenance...with all of those inaccessible surfaces.]
That having been said, there were a couple of small manufacturers (like Schilke) that never lacquered their instruments...but (in particular) Schilke trumpets - with no silver to cover up the base metals - are fabricated of such a hodge-podge of metals, that (well...) they look "goofy" without silver unifying their appearance.

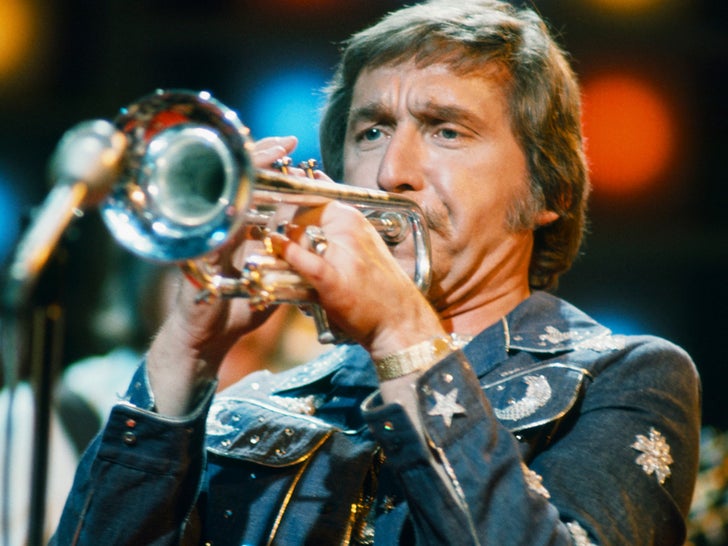