I need a small project…
- the elephant
- Posts: 3999
- Joined: Thu Aug 13, 2020 8:39 am
- Location: Yazoo City, Mississippi (stop laughing!)
- Has thanked: 2378 times
- Been thanked: 1770 times
Re: I need a small project…
It mounts to the ways with a vertical table. This gives you the X, Y, and Z axes. If it is designed well a milling attachment can be very handy. The end mill goes into the chuck and the workpiece is locked to the milling vice.

- Rick Denney
- Resident Genius
- Posts: 1032
- Joined: Thu Aug 13, 2020 8:24 am
- Has thanked: 57 times
- Been thanked: 335 times
I need a small project…
The milling attachment mounts on the cross slide instead of the compound, and provides a vertical screw and vise. Mine was made for the 16” lathe so I need to make an adapter. But it’s heavier and stiffer, too. It’s no replacement for a mill, but it will make things possible for those who don’t have a mill. And if you need to mill the end of a long shaft, such as to put a cross slot in it, good luck with that on a vertical knee mill.
Mine weighs 70 pounds.
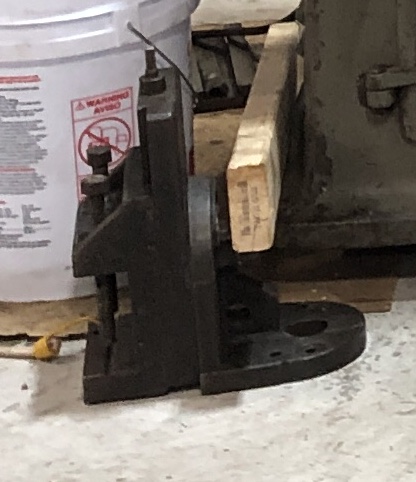
This is clipped from a much larger photo so it’s hard to see. The vise is on the left, and the vertical screw pulls it on vertical dovetail ways. The horizontal base mounts on the cross slide. You use a collet chuck and mount an end mill (or whatever tool) in the spindle of the lathe. Then, the cross slide power feed drags the work piece in the vise across the spinning tool. It’s not rigid enough to take more that light cuts.
You can mount it at angles to square up the surface to be milled to the tool, even if it’s not parallel to the vise jaws.
The vise is not super precise as one would want on a mill table, so setup is tedious to dial in real accuracy. One spends a lot of time measuring things with a manual lathe.
Rick “but it does work” Denney
Mine weighs 70 pounds.
This is clipped from a much larger photo so it’s hard to see. The vise is on the left, and the vertical screw pulls it on vertical dovetail ways. The horizontal base mounts on the cross slide. You use a collet chuck and mount an end mill (or whatever tool) in the spindle of the lathe. Then, the cross slide power feed drags the work piece in the vise across the spinning tool. It’s not rigid enough to take more that light cuts.
You can mount it at angles to square up the surface to be milled to the tool, even if it’s not parallel to the vise jaws.
The vise is not super precise as one would want on a mill table, so setup is tedious to dial in real accuracy. One spends a lot of time measuring things with a manual lathe.
Rick “but it does work” Denney
- These users thanked the author Rick Denney for the post:
- the elephant (Sun Jan 08, 2023 6:43 am)
- arpthark
- Posts: 4715
- Joined: Mon Aug 24, 2020 4:25 pm
- Has thanked: 1259 times
- Been thanked: 1402 times
Re: I need a small project…
Hmm, yes. I recognize some of these words.
- Rick Denney
- Resident Genius
- Posts: 1032
- Joined: Thu Aug 13, 2020 8:24 am
- Has thanked: 57 times
- Been thanked: 335 times
Re: I need a small project…
Here’s a pic of the lathe with more context.matt g wrote:[mention]Rick Denney[/mention], I’m hoping you post some more pics just so people can see the scale of that lathe!
It’s nominally a 6-foot bed, but that’s the whole bed. It will turn 38” between centers. The 14-1/2” dimension is the swing—the largest diameter that can be turned without running into the ways. The chuck is 10” in diameter. It takes up about three feet by seven feet of floor space.
I just today installed a hoist and trolley to help handle the big 4-jaw chuck and the milling attachment. I’m running it in Unistrut, which will carry 600 pounds, using an old Jet half-ton chain hoist.
Rick “<$100 for the hoist and trolley—Joe would be proud” Denney
- These users thanked the author Rick Denney for the post:
- the elephant (Sun Jan 08, 2023 6:47 am)
- Rick Denney
- Resident Genius
- Posts: 1032
- Joined: Thu Aug 13, 2020 8:24 am
- Has thanked: 57 times
- Been thanked: 335 times
Re: I need a small project…
When I get it set up I’ll show some pics.arpthark wrote:Hmm, yes. I recognize some of these words.
Rick “need to machine an adapter” Denney
- bort2.0
- Posts: 5303
- Joined: Thu Aug 13, 2020 9:13 am
- Location: Minneapolis
- Has thanked: 342 times
- Been thanked: 1028 times
- Rick Denney
- Resident Genius
- Posts: 1032
- Joined: Thu Aug 13, 2020 8:24 am
- Has thanked: 57 times
- Been thanked: 335 times
Re: I need a small project…
The new shop is definitely bigger than my house.bort2.0 wrote:Your garage looks bigger than my house
Rick “ whole other topic” Denney
- These users thanked the author Rick Denney for the post:
- bort2.0 (Sun Jan 08, 2023 9:45 am)
- bort2.0
- Posts: 5303
- Joined: Thu Aug 13, 2020 9:13 am
- Location: Minneapolis
- Has thanked: 342 times
- Been thanked: 1028 times
Re: I need a small project…
Right on!Rick Denney wrote: Sun Jan 08, 2023 5:05 amThe new shop is definitely bigger than my house.bort2.0 wrote:Your garage looks bigger than my house
Rick “ whole other topic” Denney

-
- Posts: 409
- Joined: Thu Aug 13, 2020 12:38 pm
- Has thanked: 34 times
- Been thanked: 62 times
Re: I need a small project…
Project suggestion:
Valve stem, button and top valve cap for horn of your choice. Button can be all metal or with pearl inlay. Extra points for making bottom cap. The same setup to make the top cap will probably work for the bottom cap. Knurl the edges of buttons and caps? It's your project, man...
These parts can get a horn missing them back in action. Buy them from Allied, you say? Allied won't sell to you and, besides, the horn is old and no parts are available.
Valve stem, button and top valve cap for horn of your choice. Button can be all metal or with pearl inlay. Extra points for making bottom cap. The same setup to make the top cap will probably work for the bottom cap. Knurl the edges of buttons and caps? It's your project, man...
These parts can get a horn missing them back in action. Buy them from Allied, you say? Allied won't sell to you and, besides, the horn is old and no parts are available.
- Rick Denney
- Resident Genius
- Posts: 1032
- Joined: Thu Aug 13, 2020 8:24 am
- Has thanked: 57 times
- Been thanked: 335 times
Re: I need a small project…
Yeah, buttons, stems and caps are on my list. Stems are easy. Buttons are moderately easy, if I can find a thread die that will work. Caps are possible, but only if the threads are inch-based. My lathe doesn’t do metric threading, though it will single-points threads as fine as 224 threads/inch.
Knurling is not difficult on this lathe, especially in brass or nickel-silver.
Rick “making two that look alike may be tricky :)” Denney
Knurling is not difficult on this lathe, especially in brass or nickel-silver.
Rick “making two that look alike may be tricky :)” Denney
- These users thanked the author Rick Denney for the post (total 2):
- the elephant (Sun Jan 08, 2023 4:51 pm) • The Big Ben (Sun Jan 08, 2023 10:53 pm)
- bloke
- Mid South Music
- Posts: 21437
- Joined: Thu Aug 13, 2020 8:55 am
- Location: western Tennessee - near Memphis
- Has thanked: 4482 times
- Been thanked: 4792 times
Re: I need a small project…
I predict that you will eventually retrofit with a computer...or perhaps not. 
- Rick Denney
- Resident Genius
- Posts: 1032
- Joined: Thu Aug 13, 2020 8:24 am
- Has thanked: 57 times
- Been thanked: 335 times
Re: I need a small project…
Installing digital readouts isn’t an impossibility, but not before I’ve run out of stuff to learn using dial indicators and micrometers. My backlash on the newly rebuilt cross slide is only 0.008, so it’s easy to manage.bloke wrote:I predict that you will eventually retrofit with a computer...or perhaps not. [emoji3]
Rick “and a linear track on the bed would interfere with the taper attachment” Denney
- These users thanked the author Rick Denney for the post (total 2):
- the elephant (Tue Jan 10, 2023 9:22 am) • bloke (Tue Jan 10, 2023 9:34 am)
- bloke
- Mid South Music
- Posts: 21437
- Joined: Thu Aug 13, 2020 8:55 am
- Location: western Tennessee - near Memphis
- Has thanked: 4482 times
- Been thanked: 4792 times
Re: I need a small project…
Arbitrary statements and predictions prevent my posts from being incorrect. 
- Rick Denney
- Resident Genius
- Posts: 1032
- Joined: Thu Aug 13, 2020 8:24 am
- Has thanked: 57 times
- Been thanked: 335 times
I need a small project…
Wade, I’ve just pulled the spindle on my craptastic drill press with the idea of correcting the runout, at least to some extent. If I am successful, I will let you know.
The plan is a Morse #2 reamer in a toolpost holder in the lathe, and spinning the spindle in the lathe. That should ensure concentricity, if the reamer will stay straight and not follow the hole too much. The concern is opening the taper too much making arbors sit too deeply. Gonna hafta go slow.
And the drill press spindle may be hardened too much. Haven’t tested that yet.
Alternatively, I could single-point skim the taper using a boring bar. But that’s less of a beginner attempt.
The worst that can happen is I ruin the drill press, but I can probably make a new spindle from scratch and get someone to weld on the pulley spline. The drill press is fairly useless now, though, with .060 runout at the tip of the chuck (it’s not the chuck and the bearings are tight).
Your drill press wasn’t as bad as I recall and may be easier to fix.
Rick “on the granite surface table getting measured now” Denney
The plan is a Morse #2 reamer in a toolpost holder in the lathe, and spinning the spindle in the lathe. That should ensure concentricity, if the reamer will stay straight and not follow the hole too much. The concern is opening the taper too much making arbors sit too deeply. Gonna hafta go slow.
And the drill press spindle may be hardened too much. Haven’t tested that yet.
Alternatively, I could single-point skim the taper using a boring bar. But that’s less of a beginner attempt.
The worst that can happen is I ruin the drill press, but I can probably make a new spindle from scratch and get someone to weld on the pulley spline. The drill press is fairly useless now, though, with .060 runout at the tip of the chuck (it’s not the chuck and the bearings are tight).
Your drill press wasn’t as bad as I recall and may be easier to fix.
Rick “on the granite surface table getting measured now” Denney
- These users thanked the author Rick Denney for the post:
- the elephant (Fri Jan 13, 2023 10:59 am)
- the elephant
- Posts: 3999
- Joined: Thu Aug 13, 2020 8:39 am
- Location: Yazoo City, Mississippi (stop laughing!)
- Has thanked: 2378 times
- Been thanked: 1770 times
Re: I need a small project…
On mine, the two parts are one, and not replaceable. I will eventually get a more accurate drill press.
And a lathe.
And a mill.
Oy…
And a lathe.
And a mill.
Oy…


- Three Valves
- Posts: 4814
- Joined: Thu Aug 13, 2020 4:07 pm
- Location: The Land of Pleasant Living
- Has thanked: 912 times
- Been thanked: 540 times
Re: I need a small project…
I though it was a combination pot belly stove, sewing machine and hit and miss engine with a power take off attachment.bort2.0 wrote: Fri Jan 06, 2023 7:02 pm Okay, move this to the other side of the railyard.
(It's a locomotive engine, right?)

Thought Criminal
Mack Brass Artiste
TU422L with TU25
1964 Conn 36k with CB Arnold Jacobs
Accent (By B&S) 952R with Bach12
The Fourth Estate is the Fifth Column
Mack Brass Artiste
TU422L with TU25
1964 Conn 36k with CB Arnold Jacobs
Accent (By B&S) 952R with Bach12
The Fourth Estate is the Fifth Column
-
- Posts: 1611
- Joined: Thu Aug 13, 2020 10:39 pm
- Location: SoCal
- Has thanked: 1871 times
- Been thanked: 568 times
Re: I need a small project…
Too true!Rick Denney wrote: Sun Jan 08, 2023 2:22 pm Rick “making two that look alike may be tricky :)” Denney
Some old Yorks, Martins, and perhaps a King rotary valved CC
- Rick Denney
- Resident Genius
- Posts: 1032
- Joined: Thu Aug 13, 2020 8:24 am
- Has thanked: 57 times
- Been thanked: 335 times
I need a small project…
I was reasonably successful. I ended up machining the JT3 chuck taper to avoid opening up the Morse taper in the spindle too much. That would work with yours, too. I chucked up the top bearing journal in a 4C collet in the lathe spindle, and used the steady against the bottom bearing journal and indicated it in. I then machined a new taper that goes in the chuck. The arbor is now off-center but it corrects the error in the spindle.the elephant wrote:On mine, the two parts are one, and not replaceable. I will eventually get a more accurate drill press.
And a lathe.
And a mill.
Oy…
Total runout at the chuck us now 0.006, which is probably the chuck.
The arbor just has to go in the right way from here on out. I ground in some markers to make that easy.
Rick “good enough for a drill press” Denney
- These users thanked the author Rick Denney for the post (total 2):
- the elephant (Sat Jan 14, 2023 10:00 pm) • bloke (Sun Jan 15, 2023 8:55 am)
- bloke
- Mid South Music
- Posts: 21437
- Joined: Thu Aug 13, 2020 8:55 am
- Location: western Tennessee - near Memphis
- Has thanked: 4482 times
- Been thanked: 4792 times
Re: I need a small project…
...so how fast do you think you could knock out a few thousand .223 shells for personal use?
https://www.theepochtimes.com/mkt_app/l ... 85869.html
https://www.theepochtimes.com/mkt_app/l ... 85869.html