Page 1 of 2
Cutting Thick Brass — SOLVED!
Posted: Sun Jan 09, 2022 9:51 am
by the elephant
So I have this bar of .25" thick NS and I cannot figure out how to neatly cut a curve into it. A scroll saw does not have the gust (and is designed for use with wood, so the stroke is way too short to do much more than wear out and snap blades like crazy). A band saw needs a blade that is too wide (front to back) to cut metal that thick and still be able to make the needed curve.
I guess I need to buy a coping saw and spend a few days with it because that is how long it will take to cut this curve by hand. and then, because of it being a free saw, it will be very difficult to keep the curve perpendicular to the surface of the metal, or even keep to the cut line on both faces at the same time.
I think I need to make a special miter box that will keep the saw still and allow me to rotate the piece around the curve, but I am having trouble "seeing" that in my head.
Suggestions? Willson makes these, but they are not the correct size and shape for my hand, so I need to sort of copy that part using the dimensions I need — but how does he even cut these parts? I am not into the idea of sand casting here at my house, but casting may be how he is making these things. He could use a laser cutter, but that technology was not available when these were being made for the earlier Kurath instruments.
Maybe I need to visit a local machine shop and see if they can cut the piece for me. It is frustrating when I cannot figure something like this out on my own.

Re: Cutting Thick Brass — WTH?
Posted: Sun Jan 09, 2022 2:06 pm
by bloke
> "Chunk" out (my commercial artist Mom's term) the piece outside of your line (regular hack saw / skinny hack saw / etc...don't waste jeweler's saw blades).
> Find the crap that came with your grinder, install that (most-of-the-time: useless) table, and install it right at the 9 o'clock "tangent point.
> Grind off the excess nearly to your line.
> Take one last very careful/slow pass, coming as close to your line as you dare (based on how easy it is to control).
> File down the edge, correcting slight imperfections and smoothing the edge.
> If there happened to have been a minor slip-up or two, fill in with silver braze and file that.
If you wish to imitate that Willson plate-thing, you might decide to go back (turning your object on it's side) and (free-handedly) grind a concave symmetrically-curved rut (imitating the curvature/o.d. of that 1st slide circuit tubing elbow) into the inside curve. This (as the diameter of your grinding stone is obviously too large) would probably best be done with a Dremel. Were it me, I might choose to put the Dremel tool in a vice, rather than your piece of brass. This would certainly improve final appearance, and eliminate a whole bunch of annoying/not-good-looking silver-braze "filling in" - when attaching that inside curve to the sheet metal flange (which you plan to cut out of the curve of a slide bow or elbow).
Dave Surber at Getzen would take your order for the Swiss-made part, but (likely: agreeing with you, guessing at your tack and p.o.v.) it would take too long and cost too damn much.
important note:
If ALL of this is off-base and NONE of it is helpful, please make some scratch cornbread, and dip it in buttermilk. Otherwise, please consider Oreos and regular whole milk.
Re: Cutting Thick Brass — WTH?
Posted: Sun Jan 09, 2022 5:24 pm
by the elephant
I don't know what you mean about the grinder "table". My Makita does not have any attachments other than a reversible handle. As far as hogging out that piece inside the curve radius I had already planned to do that. (I have way more of this ridiculously thick bar than I could ever use, so wastage is not an issue.) And I had planned to radius the inside of the curve to fit the tubing "foot". I don't know how to make the curve cut clean and flat before the radius work. I am pretty good at that sort of eyeballing but want/need the part to fit the knuckle of the valve really well before I begin that, or I will never get it to fit nicely. And I still have all of the remaining edges to cut. What do I use to simply make clean cuts through heavy NS bar stock? Again, a scroll saw will not do it. My machinist friends are all telling me to buy a dry-cut chop saw, but I just need this for like an hour. Likewise, my metalworking friends suggested this special scroll saw-like tool made especially for what I need to do, but it is like $2,400, so a big-a$$ NOPE to that suggestion!
I guess I will rough-cut as much as I can with the Makita, then move to my Dremel with these nice 2" fiberglass-reinforced wheels. I found a nice arbor for them that fits my Dremel chuck, and now that I think of it, these could be pretty helpful, but I have no idea how to make the inside edge look "nice" or at least not brutalized.
Can you tell I do not make much with thick bar stock? I do not have anything that will work, and my idea about using a scroll saw with jewelers saw blades can be done, but I would snap like 50 blades doing this, because the cutting would be confined to about .75" of the toothed part of the blade, wearing it out very quickly.
I am an idiot.

Re: Cutting Thick Brass — WTH?
Posted: Sun Jan 09, 2022 5:33 pm
by bloke
You aren't any sort of idiot, and the absolute opposite of incompetent, as well.
Cleverly, you're asking for suggestions.
I call this a "table", but it may be a misnomer:
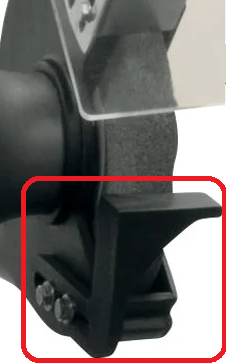
- table for a gringing wheel.png (70.25 KiB) Viewed 1309 times
If you're like me, it (as well as the bullcrap "shield") is/are still in the old decaying original box (in the attic).
If you're going to grind out that inside curve to a concave thingie, you'll probably want to take this "table" thing back off, and toss it back in the carton.
Makita...??
Oh...OK...I'm referring to a grinding wheel on a floor stand.
Re: Cutting Thick Brass — WTH?
Posted: Sun Jan 09, 2022 5:34 pm
by UncleBeer
I can't picture the part you're making, but I'm with Bloke re: grinding wheel, and then files as needed.
Re: Cutting Thick Brass — WTH?
Posted: Sun Jan 09, 2022 5:37 pm
by bloke
If you have a old funky grinding wheel (with worn-down corners) that particular one might be idea for making the concave shape on that inside curve (and I'm still assuming that you're copying the Kurath part).
ok...yeah...Some people call these "bench grinders", but I don't have one mounted on a "bench"...Mrs. bloke has a TINY one mounted on a bench (held by a couple of little-bitty clamps), but mine are both on floor stands - in the buffing room...so not "bench". (sorry for any confusion

!)
Re: Cutting Thick Brass — WTH?
Posted: Sun Jan 09, 2022 8:48 pm
by the elephant
I'll have to go to Commie Freight and pick up a grinding stone. The only thing that popped into my head when you said "grinder" is "angle grinder" as I have never owned or used a grinding wheel.
I have an old Chinese buffer motor with something wrong with it that I *might* be able to fix. I can slap a grinding wheel on that. If that fails to work I could mount one on one side of my little Baldor buffer. But the two have different arbor diameters, so I would have to buy two wheels. Maybe they have a super cheap, five-or-six-uses-then-BOOM grinder I could get for not much more than the stones themselves.
Time for some Retail Therapy…
THANKS!
Re: Cutting Thick Brass — WTH?
Posted: Sun Jan 09, 2022 8:55 pm
by the elephant
This might do it for me! Also, I own three or four air die grinders with cut-off wheels or stitched cotton buffs on them. They *must* make grinding stone wheels for these. If they are about 2" that would be perfect for my needs.
Thanks again!

Re: Cutting Thick Brass — SOLVED!
Posted: Sun Jan 09, 2022 9:18 pm
by the elephant
Okay, so the wife and I will head on down to HF tomorrow to look at grinding wheels for an angle die grinder or get one of the little $35 grinders I posted above.
I will hog out the bulk of the corner inside the curve with a Dremel using the large non-Dremel wheels I have for automotive work. I will make the straight cuts with that, too. I will do the rough shape of the inside curve with the grinder machine. I will use a tiny Dremel sanding drum to clean everything up with, and then my tone hole files to smooth the straight edges and wing it on the inside curve, as that only needs to seem to be a nice face because the foot will be silver soldered to it.
I wish I had a much thicker piece for the foot, but cannot imagine finding something more than a millimeter thick that is that same pair of radii. A hunk of slide crook ought to do it if it fits pretty well. I am pretty sure the MTS crook from a 180 F will fit over that long knuckle fairly well, without too terrible of a gapping issue to have to clean up.
I might be able to make this well enough to not look like something made by a middle-aged fat guy in his carport.

Re: Cutting Thick Brass — SOLVED!
Posted: Sun Jan 09, 2022 11:21 pm
by bloke
I don’t know if you have already bought that one, but you might want to look around on craigslist - or blah blah - or get on next-door and ask if someone around you has an old grinder - with a floor stand - that they don’t need anymore.
What if you could get one that’s more of a hoss for about the same money?
Larger diameter stones are a little bit more pleasurable to work with.
If you remove all of those guards, that you can probably fit larger stones on to that machine, but I don’t know if that motor will handle them.
I realize that looking around delays your project, but people really do “have stuff”. At auction, I picked up a remarkably nice three-phase machine with a big grinder on the left side and a totally enclosed arm with a buffer on the right side. There was some other piece of crap on the same pallet, and I bid a total of $75. I don’t even know what the other piece of crap was…well I actually I do, but I had no use for it. Someone walked up to me and said they arrived at the auction late and missed bidding on it. They offered me $200 for the other thing, so I got my three phase buffer grinder for free, and used the other dough to buy a three phase converter from Grainger.
(The story regarding my E-flat tuba is similar, but I digress.)
Re: Cutting Thick Brass — SOLVED!
Posted: Mon Jan 10, 2022 6:27 am
by York-aholic
I agree. Used bench grinders aren’t difficult to find (at least here, but I can’t imagine it’s any different there).
Re: Cutting Thick Brass — SOLVED!
Posted: Mon Jan 10, 2022 7:55 am
by bloke
I wonder if you could just buy a stone (grinding wheel) that would fit on your buffing machine. You wouldn’t have the little work surface, but a larger stone/wheel is just nice to use, and it would possibly cost less than $35.
If your existing buffer is bench mounted (??), you could possibly improvise a flat work surface in front of it - made of scrap lumber, etc.
Re: Cutting Thick Brass — SOLVED!
Posted: Mon Jan 10, 2022 8:36 am
by UncleBeer
A piece of hard-won advice: keep a container of water nearby to dunk the piece in, cuz the grinding wheel will heat it up pretty quickly.
Re: Cutting Thick Brass — SOLVED!
Posted: Mon Jan 10, 2022 11:06 am
by the elephant
UncleBeer wrote: ↑Mon Jan 10, 2022 8:36 am
A piece of hard-won advice: keep a container of water nearby to dunk the piece in, cuz the grinding wheel will heat it up pretty quickly.
I usually wear MIG welding gloves when soldering, buffing, or grinding. Setting up a bucket of water is just one more thing that has to be dragged out, set up, cleaned off, and taken back inside when I am done. I work outdoors, unfortunately. I have a quenching tank for heat treatments, but I don't generally use it. Thanks, though. I have had many blisters from small burns while pulling apart heated joints that were hammered together before soldering. I
hate being burned.

Re: Cutting Thick Brass — SOLVED!
Posted: Mon Jan 10, 2022 11:25 am
by the elephant
There is exactly ONE bench grinder on craigslist, and it is THREE HOURS from me, meaning six hours in the 16 mpg jeep. It is a Chinese brand, looks clapped out, and a new one would cost less as I can spend $20 on gas + the price, versus $60 on gas + the EIGHTY BUCKS this insane man in Corinth wants for his clapped-out POS grinder.
I am going to look for a stone for my Baldor. The old Harbor Freight buffer is not going to cut it, pun intended. I have to check the arbor size of my Baldor and then shop around online. If HF carries a 6" wheel with the correct hole size I'll make the $20 drive down there to pick one up. (I am permanently stuck driving my 16 MPG Jeep now, so all purchases factor in the $20 minimum gas consumption and I have to piggyback errands in Jackson to get them done in one, long trip. Reality. Huh…)
Looking now…
Also, I finally discovered what the tool I had envisioned using for this is called. And there are several very good consumer-grade units for sale. But all are over $400, so I need to justify how often I would use this tool versus how much I would have to drop to get one. They are called ring saws, and the type I need (benchtop, liquid blade cooling, work light) is a common tool in the shop of someone who makes stained glass windows. They are like a band saw but use a diamond-impregnated wire ring that spins so that you can cut in all directions at any time. They cut thick brass pretty well, too, if you take your time. I have used one, so that was why my initial idea did not worry about how to cut the part. It never entered my mind that it would be so difficult to find this tool or that it would be so expensive.
Any ring saws that function like these that are beyond consumer-grade (meaning made out of metal, not junky, not cheesy-looking) cost thousands of dollars. So these are not very common, I guess.
I get myself into these situations all the time. You would think I would know better by now.
• Have an idea to fabricate something.
• Buy materials needed to fabricate something.
• Never consider HOW to fabricate the parts needed to make the thing.
• Discover that this is not something people normally do.
• Discover that the needed tools are both uncommon and expensive.
• Start over with a new idea.
<sigh>
Re: Cutting Thick Brass — SOLVED!
Posted: Mon Jan 10, 2022 12:12 pm
by Rick Denney
A drum sander on a drill press* might work if small enough for the inside radius.
*drill press can = power drill clamped in vice for this purpose.
Rick “but bench grinders are cheap and generally handy” Denney
Re: Cutting Thick Brass — SOLVED!
Posted: Mon Jan 10, 2022 1:27 pm
by the elephant
I think I have this fully sorted now. I'll post about this in the Kurath thread.
Thanks, all!
Re: Cutting Thick Brass — SOLVED!
Posted: Mon Jan 10, 2022 2:39 pm
by bloke
postscript
yeah...general comment about stuff, not directed at anyone
Learning is one of the things that keeps me from being completely bored with fixing horns.
It doesn't happen with most repair gigs, but it happens sometimes.
I do have a crappy dollah-stoe plastic ice cream bucket (with an inch of water in it) setting on a separate stand - next to my "main squeeze" floor-mounted grinder. I learned to have that after watching James Keyes - friend, and (mostly retired) master bassoon repairer-enhancer, and (necessarily) machinist. I even learned to put a little bit of bleach into the water, because mold is gross. (Without bleach, it's "bleech".)
Re: Cutting Thick Brass — SOLVED!
Posted: Fri Jan 14, 2022 8:42 pm
by Matt Walters
If you want to machine a perfectly round piece, cut out a hexagon a bit oversize. Solder it to brass rod in the middle. Chuck the rod in the lathe. Then use a cutting tool to cut off the outside edge until it is round and then down to size. Unsolder the brass rod, buff the nickel and there you go.
Re: Cutting Thick Brass — SOLVED!
Posted: Fri Jan 14, 2022 9:06 pm
by the elephant
Thanks! However, I do not yet own a fully functional lathe. (No tailstock.) The parts are hard to find, but I am looking in the UK for one with imperial graduations and leadscrews. Most of them are metric, which is of no use to me since all my leadscrews and dials are imperial. I'll get it, though.)
Also, I need to cut an irregular INSIDE curve in the bar stock to have it fit up next to a long knuckle on my 1st valve. The problem was (mostly) that I was thinking I could salvage the hunk I was going to remove. I know now that with my tools I cannot do this, but I *can* just hog most of the material out and *then* "prettify" the curved edge.
I will get this done, somehow. Thanks very much for taking the time to help me out, though, Matt.